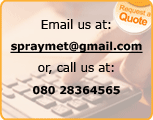 |
Coatings Range
Carbide coatings
Wear resistant hard facing materials
Typical thickness of 0.1 to 0.5mm
Extremely hard coating materials 65-72 RC (900-1300Hv)
Very dense >99%
Smooth coatings of typically 3 to 4 Microns Ra as sprayed
finish
Outstanding adhesion with HVOF-applied coatings generally
>10,000 psi bond strength
Applied by HVOF and HP/HVOF
Hard Chrome plating replacement
Can be ground to a 0.4 Microns Ra surface finish, or super
finished to 0.1 Micron Ra
Common Coatings:
Tungsten Carbide : WC/Co, Wc/Ni, Wc/Co/Cr, Wc-CrC-Ni erc
Chrome Carbide : Cr3C2, Cr3C2/NiCr
Titanium carbide
Ceramic Coatings
Ceramics applied by Plasma spray are used for
Dielectric strength
Sliding wear
Thermal barriers
Corrosion protection
Typical thickness of 0.1 to 0.7mm
Hard ceramic coating materials, 60-68 HRC
Very dense to porous depending on application requirements
Excellent adhesion
Can be ground to a 0.4 Ra surface finish, or superfinished to
0.1Ra.
Common Coatings:
Aluminum Oxide, : Al2O3, Al2O3/ 3TiO2, Al2O3/ 13TiO2,
AlO3/40TiO2)
Chromium Oxide: (Cr2O3 , Cr2O3+TiO2+SiO2) Highest hardness
Titania (TiO2)
TBC : Yttria stabilized Zirconia ( thermal barrier coatings,
ZrO2-8% Y2O3)
Zirconia : (Ca or Mg Zirconium Oxide )
Metal and Metal Alloy Coatings
Metal alloys can be used as bond coatings for other thermal
spray coatings
Nickel and Ni alloys such as NiAl are commonly used for
dimensional buildup of parts for ease of
machining
Stainless steel, NiCr, etc. can be used to restore dimensions
or to put an improved surface for wear and
corrosion.
Stellite, Triballoy, and other tribological materials can be
used for improved performance over an easily
fabricated base material.
Molybdenum (Mo) and other refractory metals can be used for
high temperature wear resistance, for sliding
wear, and applications requiring lubricity. Widely used on
automotive parts.
Cobalt (Co), Tantalum (Ta), Chromium (Cr), Tungsten (W) and
similar types of materials offer specialized
properties.
Copper (Cu) and Aluminum (Al) based materials are used for
corrosion resistance, electrical conductivity,
thermal conductivity, and other applications
MCrAlYs, such as CoCAlY, NiCrAlY, CoNiCrAlY and NiCoCrAlY,
are used for hot oxidation protection and
corrosion protection in gas turbine applications and in high
temperature wear and corrosion up to 1000°C.
They are also excellent bond coat materials.
Common coatings:
MCrAlYs (NiCrAlY, CoCrAlY, NiCoCrAlY, CoNiCrAlY)
Nickel Aluminum alloys (NiAl) ,Nickel Chrome
Molybdenum (Mo) and Mo alloys
Titanium (Ti)
Stellite : # 1,12, 6, 20, 21
Triballoy
Ferrous alloys : SS 316, 304, 413, 420, 174Ph
Non Ferrous alloys : Cu, Al, Ph Bronze, Al Bronze, Babbitt
Abradable Thermal Spray Coatings
Our Advanced Coatings Enhance the Performance of Your Parts
by tight clearance control
These coatings are used in gas turbine engines for clearance
control. As the rotating assemblies and blades heat up and cool
down, they change in size because of thermal expansion.
Manufacturing the assemblies to achieve close clearances during
operation is difficult. The solution is to add a thick clearance
control coating to the housing. As the blades rotate and heat
up, they abrade a path through the abradable coating making a
near perfect fit groove to run in. This close fit provides low
leakage around the perimeter of the blades.
This specialized coating must be soft enough to abrade away as
desired. Yet tough and heat resistant enough to last for the
long run.
Ni-graphite, NiAl-Bentonite, Nickel-Aluminum, Aluminum
Silicon-Graphite, AlSi-Polyimide, AlSi-Polyester are common
abradable coating materials.
|